Measuring Sn Electroplate and Underplating Over Cu Alloys
Human use of tin dates back millennia to when we started alloying it with copper to produce bronze.
Today, tin has a wide variety of important uses thanks to its physical properties. Nearly half of all tin produced is for solder alone, while tin-plated steel is commonly used for food contact applications due to tin being non-toxic, non-carcinogenic, and resistant to corrosion.
Tin is also commonly used to electroplate copper and copper alloy components such as terminal pins, wires, and busbars. Its conductivity and resistance to corrosion and oxidation make it ideal to protect electrical components that will be exposed to the atmosphere. Copper is prone to oxidation that causes its resistance to rapidly increase. While tin still oxidizes, its oxide is relatively thin and keeps its conductivity high.
ASTM standard B545 gives specifications for electrodeposited tin coatings. Both bright and matte tin electrodeposits are used on copper and copper alloys. Bright tin has a smooth, lustrous finish that makes it a popular choice for coating wires and electrical contacts. However, it should not be used for soldering applications as the organic brightening additives can burn when exposed to soldering temperatures which can interfere with the integrity of the solder joint. Matte tin lacks brightening agents and is superior for solderability but has a coarser grain structure that leads to a greater insertion force.
Thickness of the electrodeposit is critically important for the performance of the electroplating. As thickness decreases, the porosity increases, which can dramatically impact the protective function of the deposit. For products such as electrical spring contacts, too thick a deposit can negatively affect the mechanical operation.
B545 specifies minimum thickness for tin electrodeposits of certain classifications. For example, service class A, intended for electrical contact services in mild environmental conditions, requires a minimum of 2.5µm (100µin) of tin electroplating. Additionally, some applications require an intermediate layer between the tin and the substrate called an underplate. Tin plated over brass requires an underplate of copper of at least 2.5µm (100µin) or nickel of at least 1.3µin (50µin) to prevent zinc from diffusing into the tin and impairing the plating. Manufacturers may have their own thickness specifications for their tin-electroplated components.
To monitor thickness of tin electrodeposits and underplates, many manufacturers along each step of the process turn to x-ray fluorescence (XRF) spectrometry to quickly and reliably measure thickness of each plating layer simultaneously. XRF works by exciting the elements in the surface of the component so that they emit their own characteristic (unique to each element) x-rays. The intensity of these x-rays can be used to calculate the thickness of the plating.
Older generation tools often struggled with elements common to each layer, such as a copper underplate over brass (copper-zinc) alloy or tin deposited on bronze (copper-tin). New generation hardware effectively mitigates this issue.
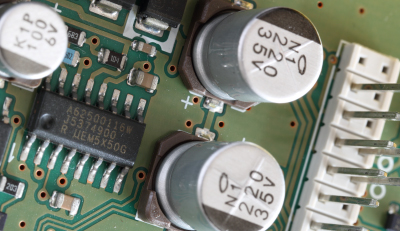
Learn more about how XRF can measure tin electroplating on copper alloys in our latest applications note!
Conclusion
Bowman B, P, L, and K series are ideal tools for quickly and precisely determining thickness in tin electroplating and copper and nickel underplate. High resolution silicon drift detectors and Archer software greatly reduce common element interference from copper alloy substrates affecting the readings of the thickness layers above. With a user friendly and feature-rich Archer software, Bowman XRF systems are the ultimate one-stop solution for thickness measurement, elemental and plating bath analysis. Call our support team for more information.