Measuring Carbide Elemental Composition
Approximately 60% of the world's tungsten production is for the manufacture of cemented carbide cutting tools. Tungsten metal reacts with carbon at high temperatures to produce tungsten carbide (WC) powder, which is then compacted and fused together with a binder metal – typically cobalt – into various shapes and sizes in another high temperature process called sintering. The resulting composite material has high hardness, toughness, and resistance to wear and temperature. Compared to prevalent tool steels, carbide can operate at higher speeds and lasts longer.
The properties of the cemented carbide can be adjusted by varying the relative composition of the carbide particles (the hard phase) to the binder metal (binder phase). The carbide phase typically makes up 70-97% of the composite by weight, with higher carbide content generally increasing hardness and wear resistance, and higher cobalt content increasing toughness and shock resistance. Composition also significantly affects the thermal behavior of the cemented carbide composite, meaning that different ratios of the hard and binder phases can be used to optimize the carbide composite for different operating temperatures.
Tool makers who want to ensure that their carbides have the appropriate ratio of hard phase and binder phase for the intended application are presented with a challenge – the desired refractory properties of carbide composite also make it very difficult to process as needed for destructive test methods such as cross-sectioning, titration, AAS, and ICP.
Fortunately, X-Ray Fluorescence (XRF) is a test method that is fast, reliable, and requires little to no sample preparation. One of the most critical advantages of XRF is that it is non-destructive, meaning material intended for production can be analyzed directly without being consumed. A single measurement can give manufacturers an accurate composition within seconds. XRF can also accurately determine the thickness of the vapor deposited coatings on finished carbide tools, adding even further versatility to the inspection process.
All Bowman XRFs are equipped with solid state silicon drift detectors (SDD) to precisely measure thickness and composition. The latest detector developments of SDDs – Silicon Drift Detector – provide the best resolution, lowest noise level (highest S/N ratio), and shortest test times while providing accurate and reliable results.
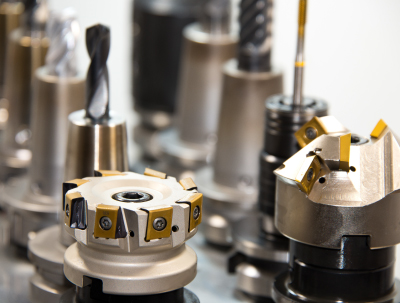
To learn more about how you can use x-ray fluorescence to monitor carbide (WCCo), read our latest application bulletin!
Conclusion
Bowman B, P, L, and K series are ideal tools for quickly and precisely determining composition of cemented carbide. XRF can also accurately determine the thickness of the vapor deposited coatings on finished carbide tools, adding even further versatility to the inspection process. With a user friendly and feature-rich Archer software, Bowman XRF systems are the ultimate one-stop solution for thickness measurement, elemental and plating bath analysis. Call our support team for more information.