Measuring Nanometers Thin PVD coatings
Physical Vapor Deposition (PVD) is a common technology used to apply thin films of materials to surfaces.
These coatings offer numerous advantages: enhanced wear, corrosion, and heat resistance, increased hardness, improved aesthetics—just to name a few. The process involves the vaporization of a solid material in a vacuum, followed by the deposition of this vapor onto the surface of substrate. Substrates can include metals, plastics, glass, ceramics, etc. There are two main methods: sputtering and evaporation. With sputtering, high-energy ions bombard and eject the target material, which then deposits onto the substrate forming a thin film. Evaporation works in a similar fashion. The target material is evaporated in a vacuum, causing particles to travel to and condense on the substrate.
PVD is highly versatile. The technique can be used with a vast number of both organic and inorganic materials, and can in many cases provides harder, more corrosion resistant coatings than traditional electroplating processes. As such, many industries including automotive, aerospace, electronics, and medical devices rely on PVD. As with any type of coating, it is imperative that the thickness of the deposition is monitored to ensure the full benefits of the coating are obtained while minimizing the amount of material waste. Specifications such as AMS 2444A outline these benefits and provide guidance on achieving the desired properties from PVD coatings.
AMS 2444A gives specifications for titanium nitride coating on metal parts applied by PVD. The coating is split into three classes based on thickness: 1.27-3.81µm thick, 2.54-6.10µm thick, and 6.35-12.70µm thick. Each class offers unique properties related to friction and lubricity, wear resistance, appearance, etc. Under or over depositing target materials can cause coated parts to lack the desired qualities and can even cause issues such as flaking and decreased durability. It is therefore critical to closely monitor deposition thickness.
XRF provides a fast, non-destructive method to analyze PVD coating thickness. Every Bowman unit is capable of measuring up to 5 thickness layers simultaneously. Additionally, PVD coating applications commonly require nanometer-level coating thicknesses to obtain the desired harness/protection while avoiding wasting expensive material. Previous generation XRF instruments relied on a gas-filled proportional detector, which do not provide reliable, accurate readings for thin coatings and coatings of low-energy materials such as Al or Ti. All Bowman XRFs are equipped with solid state silicon drift detectors (SDD) to precisely measure PVD. The latest detector developments of SDDs – Silicon Drift Detector – provide the best resolution, lowest noise level (highest S/N ratio), and shortest test times while providing accurate and reliable results.
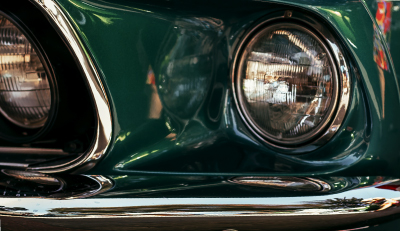
To learn more about how you can use x-ray fluorescence to monitor PVD coating thickness, read our latest application bulletin!
Conclusion
Bowman B, P, L, and K series are ideal tools for quickly and precisely determining thickness of ultra thin PVD coatings. The high resolution silicon drift detectors and advance software can accurately distinguish nanometers thick metallic layers. With a user friendly and feature-rich Archer software, Bowman XRF systems are the ultimate one-stop solution for thickness measurement, elemental and plating bath analysis. Call our support team for more information.